Mean Time Between Failure (MTBF) is a vital metric widely used across industries to gauge the reliability of components, systems, or equipment. It is a maintenance metric that measures the average duration of an equipment’s operability before any potential system failure.
A higher MTBF indicates system reliability, which helps businesses determine equipment failure frequency and reliability issues. As a core aspect of maintenance management, MTBF is essential for:
- Gauging performance
- Assessing safety
- Evaluating equipment design
- Estimating an asset’s dependability
Improving MTBF can reduce the frequency of failures, offering benefits such as improved operational efficiency and reduced maintenance costs. Continuous MTBF monitoring and optimization help organizations identify patterns and trends that may indicate underlying issues, prompting more sophisticated maintenance strategies.
Site Reliability Engineering (SRE) teams use this metric-based monitoring value to prioritize maintenance, identify infrastructure vulnerabilities, and prevent operational downtime.
This article provides effective strategies and practical tips for increasing MTBF, helping you improve system dependability and achieve a reliable MTBF.
Key Takeaways • High MTBF indicates system reliability, helping businesses determine equipment failure frequency and reliability issues. • The MTBF is an important indicator of reliability in engineering. • Maintenance practices significantly impact MTBF, improving equipment reliability and operational lifespan. • Unscheduled maintenance can increase system failures, intentionally lowering MTBF. |
Guide on Increasing MTBF
MTBF is an important indicator of reliability engineering. It originated in the aviation industry, where an aircraft failure can be fatal. Thus, the frequency of failures must be calculated and predicted for preparedness.
The MTBF calculation measures the average time a system operates without failures. Here’s how to compute MTBF:
MTBF = total uptime / Number of system failures |
For instance, a device broke down twice within 30 days:
- Total uptime: 30 days 24 hours=720 hours
- Number of system failures: 2
- MTBF: 720 / 2 = 360 hours = 15 days
Therefore, a device that went down twice within a month has a 360-hour MBTF. One system failure every 15 days indicates a high MBTF and a reliable system. Note that this calculation focuses solely on the occurrence of unscheduled maintenance, excluding routine tasks like inspections and recalibrations.
By increasing the MTBF of system components and equipment, organizations can achieve the following benefits:
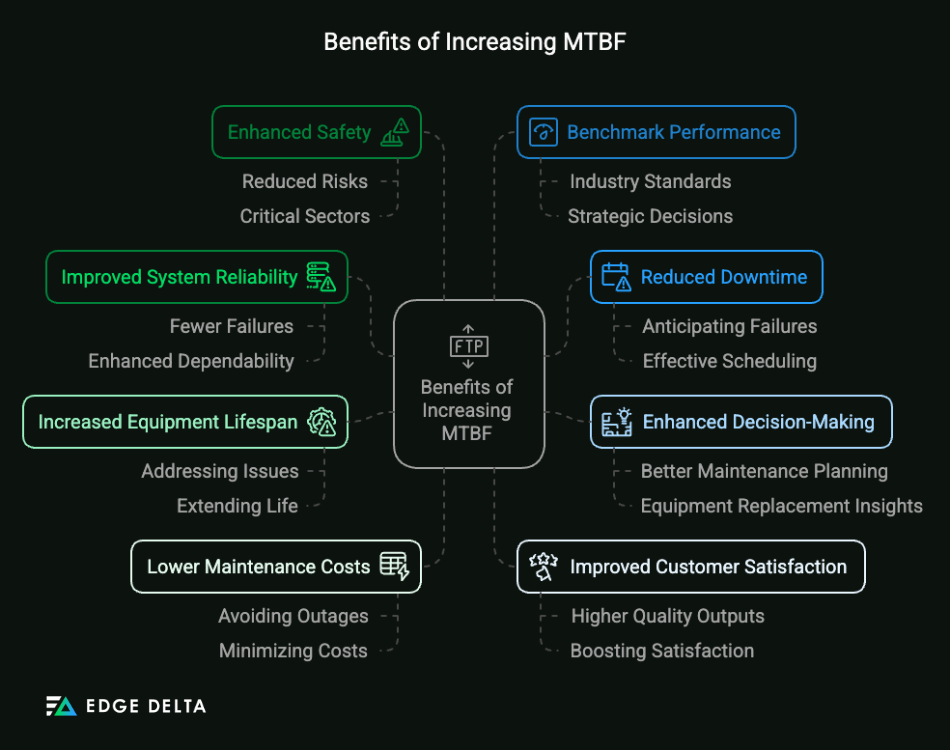
- Improved system reliability: Higher MTBF reflects fewer failures, enhancing overall dependability.
- Reduced downtime: MTBF data helps anticipate failures, thus allowing maintenance teams to schedule preventive measures effectively and reducing unexpected downtime.
- Enhanced decision-making: The calculated MTBF provides insights for better maintenance scheduling, equipment replacement, and budget planning, necessary for making informed decisions and actions.
- Increased equipment lifespan: By identifying and addressing frequent issues of systems, MTBF improvement extends the operational life of equipment, reducing capital expenses.
- Lower maintenance costs: Avoiding unscheduled outages minimizes costs.
- Improved customer satisfaction: Reliable systems produce higher-quality outputs consistently, boosting customer satisfaction.
- Enhanced safety: A higher MTBF reduces the risks associated with system or component failures, particularly in critical sectors like aerospace and healthcare where system reliability is a top priority.
- Benchmark performance: Comparing MTBF to industry standards highlights areas for improvement, guiding strategic decisions to achieve optimal performance and competitiveness.
Some real-world examples that illustrate the importance of reducing MTBF:
Electronics and semiconductors
In the electronics and semiconductor industry, MTBF assesses the reliability of repairable microchips, circuit boards, and power supplies through component design and testing.
Medical devices
In healthcare facilities, MTBF helps ensure the reliability of medical devices like scanners, testing instruments, and life-support systems, ensuring continuous medical services and reducing equipment-related incidents.
Manufacturing Industry
MTBF calculations on machines can help manufacturers spot problems and schedule maintenance or replacement before they fail, preventing costly downtime and lost productivity.
Telecommunications Sector
Network reliability is critical for providing uninterrupted communication services in the telecommunications industry. Telecommunications companies use MTBF to determine the reliability of network equipment and infrastructure.
Note Keep in mind that Mean Time Between Failures (MTBF) is an average measurement of operational reliability. It does not accurately represent the entire life cycle or longevity of an asset. |
Given the benefits and necessary applications of an increased MTFB, read on to learn various factors affecting MTFB and the best strategies and tips for improving your MTFB.
Factors Affecting MTBF
Numerous factors contribute to equipment reliability and affect MTBF, including maintenance practices and operating conditions. These factors play pivotal roles in shaping MTBF, impacting product, system efficiency, and cost.
Understanding these factors can improve system robustness, maintenance, and lifecycle management.
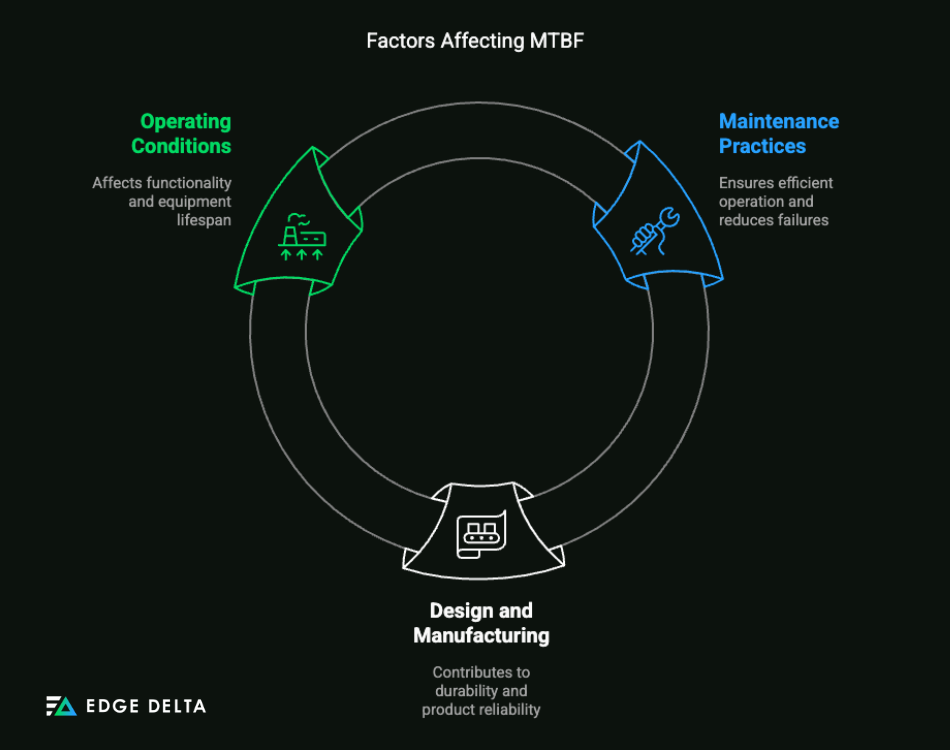
Maintenance Practices
Regular maintenance ensures systems operate within optimal conditions, preemptively addressing issues that could lead to failures. Thus, maintenance practices significantly influence MTBF, directly enhancing equipment reliability and operational lifespan.
Among maintenance strategies, preventive maintenance involves regular checks and servicing on a time or usage-based schedule to avoid failures. In contrast, predictive maintenance uses real-time data and advanced monitoring tools like vibration analysis and thermography to predict maintenance needs.
These practices allow for maintenance interventions that are precisely timed to the equipment’s condition, thus optimizing resource use and further prolonging MTBF. Combining these strategies can maximize equipment reliability and operational efficiency.
Design and Manufacturing
Design flaws and manufacturing defects heavily influence MTBF. For instance, design flaws and operation issues like poor material selection or substandard operational environment can result in frequent failures and complicated maintenance, reducing MTBF.
To mitigate these risks, robust quality control and rigorous testing are essential. Quality control helps identify and correct errors across the production lifecycle, ensuring product consistency and reliability.
Rigorous testing provides feedback for continuous improvement in design and manufacturing processes. These practices enhance MTBF, leading to higher customer satisfaction and a better brand reputation.
Operating Condition
The environment and condition in which equipment operates play a crucial role in its reliability and MTBF. Environmental factors, such as temperature regulation, dust filtration, and shock absorption, can help mitigate these factors and improve MTBF.
On the other hand, unscheduled maintenance may increase failures, deliberately lowering MTBF. Temperature, humidity, dust, and vibration can all impact equipment reliability. Therefore, regular monitoring and timely maintenance are essential to maintaining optimal operating conditions and enhancing equipment reliability.
Strategies to Increase MTBF
A higher MTBF signifies more reliable equipment, reduced downtime, lower repair costs, and improved operational efficiency. As a result, industries relying heavily on machinery and systems aim to increase MTBF. To increase MTBF, organizations must adopt a combination of strategies that enhance the durability and reliability of their systems.
Below are some of the most effective strategies to increase MTBF and ensure sustained business success.
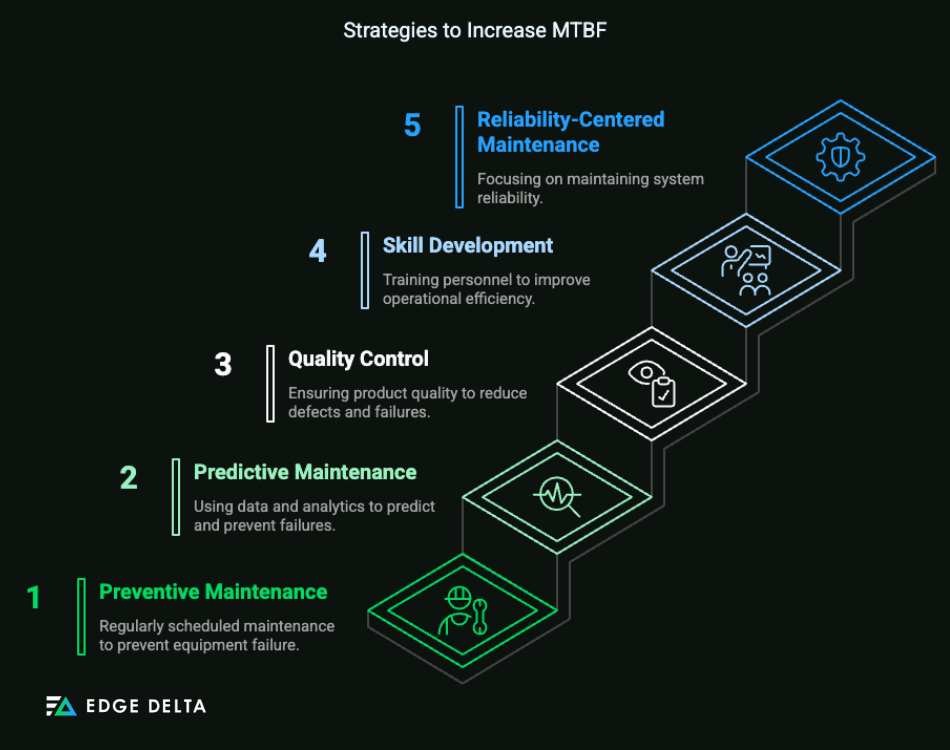
Implementing Preventive Maintenance
Preventive maintenance forms the backbone of an effective Mean Time Between Failures (MTBF) program. Managing risks before they occur helps improve asset reliability, reduce downtime, and extend failure intervals.
To achieve an effective MTBF program, begin by establishing a comprehensive preventive maintenance schedule that incorporates the following:
- Regular inspections
- Routine maintenance tasks
- Timely replacement of worn parts
For your maintenance team to work efficiently, you must provide detailed checklists and training. That includes understanding why an asset failed, which can help your team prevent or reduce future failures.
Conversely, poor training or lack of manuals and checklists can undermine preventive maintenance, causing frequent and premature equipment breakdowns.
Ultimately, being proactive rather than reactive in maintenance prevents future failures and ensures the longevity and reliability of your equipment. Thus, resulting in a more desirable MTBF.
Adopting Predictive Maintenance
Predictive maintenance differs from traditional methods by predicting equipment failures using real-time data, rather than traditional maintenance approaches that rely on scheduled or reactive maintenance. This proactive shift improves the Mean Time Between Failures (MTBF) and operational efficiency.
Additionally, predictive maintenance uses data analytics and Internet of Things (IoT) technologies. Sensors and smart devices collect detailed data on machine conditions such as temperature and vibration.
Machine learning algorithms analyze data to identify patterns and predict failure, facilitated by IoT devices that ensure timely and data-driven maintenance decisions.
Predictive maintenance provides numerous advantages that increase MTBF, including:
- Enhanced equipment reliability and reduced downtime: Predictive maintenance minimizes unexpected breakdowns by anticipating failures before they happen. This approach enhances operational reliability and reduces the Mean Time to Repair (MTTR).
- Extended equipment lifespan: Regular monitoring and timely maintenance extend the operational lifespan of machinery by preventing excessive wear and tear.
- Improved safety and risk management: Early detection of potential issues reduces the likelihood of hazardous equipment failures, enhancing workplace safety.
- Optimized maintenance scheduling: Predictive maintenance identifies the optimal maintenance times, avoiding unnecessary interventions and focusing on critical needs. Kubernetes metrics play an essential role in enhancing this approach by providing detailed insights into the operational state of the system.
- Cost efficiency: Transitioning from reactive to proactive maintenance reduces the frequency and severity of machine repairs, lowering overall maintenance costs.
Side Note MTBF is an indicator of breakdown frequency, while MTTR describes recovery time post-breakdown. These two can be used together to analyze system uptime. Ideally, a steady decrease in MTTR an increase in MTBF, and a system with minimal downtime and rapid recovery. |
Enhancing Quality Control
An enhanced quality control process is crucial in design and manufacturing as it influences product reliability and longevity. Thus, implementing stringent quality measures early helps identify and rectify potential defects, ensure product consistency, and prevent costly recalls and reputation damage.
This proactive approach builds customer trust and bolsters the company’s reputation. Here are some best practices for high-quality components and assemblies:
- Comprehensive testing regimes: Ensures that products meet high standards of performance and durability, testing should simulate real-world conditions to prevent field failures.
- Effective supplier management: Careful supplier selection and regular audits ensure high-quality materials are used, maintaining product integrity.
- Continuous improvement methodologies: Using methods like Six Sigma helps reduce variability and defects, enhancing efficiency and quality.
- Regular employee training: Ongoing training updates staff on the latest quality control technologies and practices, fostering a quality-first mindset.
- Feedback loops: Establishing feedback mechanisms with end-users and during manufacturing allows for real-time quality adjustments and meets changing customer needs.
Training and Skill Development
Maintenance goes beyond fixing problems to preserve, optimize, and extend the life of equipment and systems.
Continuous training and education can prevent common mistakes and ensure your staff can properly handle the equipment, extending its lifespan. Training and skill development create a skilled workforce that can identify, address, and prevent issues before they become costly, thus impacting MTBF.
This training provides industrial and organizational staff with the technical skills and knowledge to perform upkeep, repairs, and preventive measures. It encompasses many learning modules, including topics critical for maintaining equipment, machinery, and facilities.
Here are some tips for good training and skill development to increase MTBF:
- Focus on technical competence: Teach machinery operations, troubleshooting, and maintenance tool use.
- Incorporate safety protocols: Maintenance training covers safety procedures, risk assessment, and safety regulations to keep maintenance workers safe and ensure continuous operations.
- Understanding systems and processes: Maintenance technicians are trained to understand organizational systems and workflows, which allows them to perform maintenance without disrupting operations.
- Problem-solving techniques: Proper training allows technicians to identify system issues and solve them on the spot, reducing downtime and boosting productivity in operations.
- Feedback and adaptation: Implement a feedback system for maintenance workers to report training effectiveness and field challenges. This feedback should improve the training program to reduce equipment failures.
Using Reliability-Centered Maintenance (RCM)
Reliability-centered maintenance (RCM) optimizes maintenance programs to maintain asset functionality and longevity. RCM improves By enabling a more informed and strategic maintenance approach, RCM improves MTBF, preventing breakdowns and extending equipment life.
RCM involves a comprehensive evaluation of each asset’s criticality, operational conditions, and expected lifespan. It formulates a maintenance strategy that balances costs with productivity. It primarily incorporates preventive, predictive, and condition-monitoring methods.
The implementation of RCM involves four critical steps:
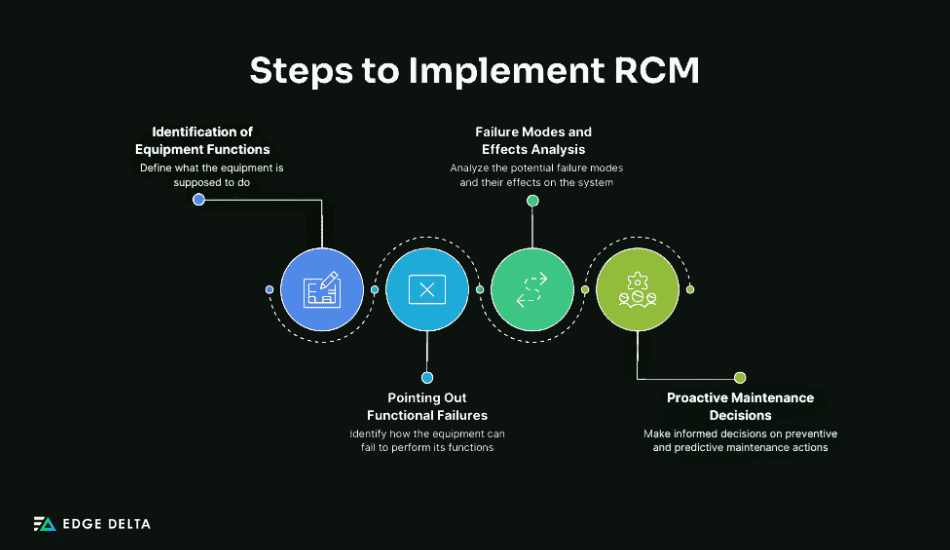
Best Practices and Tips
Increasing MTBF is crucial for enhancing the reliability and efficiency of machinery and systems. The higher the MTBF, the more reliable the equipment is considered to be. It is crucial for planning maintenance, improving product designs, and ensuring equipment reliability.
Below are best practices, along with practical tips and recommendations.
1. Regularly Updating and Reviewing Maintenance Schedules
Establish a regular schedule for maintenance checks and reviews to prevent unexpected failures and extend the life of the system, equipment, or component. An MTBF value provides a baseline for determining how to update and optimize your preventative maintenance schedule.
Knowing how often an asset could fail will help schedule the necessary maintenance to prevent failures. Similarly, it may help you perform only the essential maintenance, reducing costs and maximizing your resources.
Tips and recommendations:
- Schedule routine checks: Set up routine inspections and servicing based on the manufacturer’s recommendations and past maintenance data.
- Leverage technology: Use maintenance management software to track maintenance activities, predict when maintenance is due, and ensure no tasks are overlooked.
- Train staff: Maintenance teams need regular training sessions to stay updated on best practices and new technologies.
2. Implementing Condition Monitoring and Diagnostic Tools
Implementing condition monitoring and diagnostic tools supports predictive maintenance by tracking equipment performance in real-time. Sensors and monitoring systems. By analyzing data and trends, you can predict maintenance needs and fix problems before they break down.
Condition monitoring systems continuously check the operational status of equipment, diagnosing issues before they lead to failure. Transitioning to a condition-based maintenance approach can enhance preventive maintenance practices. This method uses real-time data to determine maintenance needs, improving reliability and efficiency with Kubernetes metrics.
Condition monitoring acts as an early warning system, identifying potential issues before they cause asset failure. Thus, it increases MTBF and reduces unplanned downtime.
Tips and recommendations:
- Select appropriate tools: Choose sensors and diagnostic tools suitable for the specific types of machinery used, such as vibration analysis for rotating equipment and thermal imaging for electrical systems.
- Data analysis: Use data analysis software to interpret sensor data effectively, enabling predictive maintenance.
- Regular calibration: Ensure monitoring equipment is regularly calibrated to maintain accuracy.
3. Conducting Root Cause Analysis for Failures
Tracing failures to their source ensures that your team doesn’t address symptoms alone. A root cause analysis (RCA) identifies the source of recurring problems. This process allows for proactive maintenance and asset management. Instead of correcting issues after they occur, you’ll avoid them in the first place.
You can conduct root cause analysis using various tools and techniques. One such powerful tool is Edge Delta, which enhances the RCA process through its advanced analytics capabilities. Though these processes may look different, they all share a common goal: fixing the root cause of an issue.
Tips and recommendations:
- Structured approach: Use a structured approach, such as the “5 Whys” method, to drill down to the root cause.
- Document findings: Keep detailed records of failures and their investigations to identify patterns or recurring issues.
- Continuous improvement: Use the findings to update operating procedures, maintenance routines, and training programs.
4. Utilizing Failure Mode and Effects Analysis (FMEA) to Identify Potential Issues
FMEA (failure mode and effects analysis) is a step-by-step method for identifying failure points on design, manufacturing, product, and service. It helps in detecting possible errors that could affect customers and in understanding the consequences of these failures. FMEA aims to:
- Ensuring all failures can be detected
- Determining how frequently a failure might occur
- Identifying which potential failures should be prioritized
Businesses typically use FMEA to facilitate analysis. For development and manufacturing organizations, FMEA effectively lowers the possible failures in phases of the product lifecycle.
Tips and recommendations:
- Engage cross-functional teams: Involve personnel from different departments (engineering, operations, maintenance) for comprehensive insights
- Prioritize actions: Use the Risk Priority Number (RPN) from FMEA to prioritize actions based on severity, occurrence, and detectability.
- Review regularly: Keep the FMEA updated with new information and operational changes.
5. On-board and Train your Operators and Technicians
Equip your maintenance and operations teams with the necessary skills and knowledge for effective equipment maintenance and operation. Regular training sessions prevent common operational mistakes, extend equipment lifespan, and enhance productivity through open communication.
Tips and Recommendations:
- Develop comprehensive training programs: Develop complete equipment operation and maintenance training modules. Incorporate new methods and technologies into these regularly.
- Implement regular refresher courses: Train team members regularly to keep skills sharp and keep them up to date on operational standards and safety protocols.
- Encourage cross-training: Promote versatility by training employees on different aspects of operations.
- Utilize mentorship programs. Pair experienced operators and technicians with new hires. Mentorship helps new hires learn and adjust faster.
- Facilitate open communication channels. Establish regular meetings and feedback loops where team members can discuss challenges and share best practices.
- Hands-on learning. Use real-world scenarios in training exercises to help team members understand the equipment and their role in maintaining it.
6. Focus on Continuous Improvement
A successful MTBF program prioritizes continuous improvement, encouraging ongoing assessment and refinement of processes, technologies, and methodologies to prevent failures and extend the operational life of equipment and systems.
Tips and recommendations to facilitate continuous improvement:
- Conduct regular reviews: Evaluate MTBF performance and identify improvement opportunities.
- Use advanced analytics: Employ analytical tools to deeply analyze failure data and identify patterns for predictive maintenance.
- Encourage feedback: Create channels for continuous input from all organizational levels and integrate insights into program enhancements.
- Benchmark industry standards: Compare your MTBF metrics with industry standards to identify performance gaps and potential improvements.
- Adopt new technologies: Incorporate the latest technological advancements in system monitoring and diagnostics.
- Iterate Improvements: Apply an iterative approach for small, manageable changes regularly, allowing for quick implementation and evaluation.
7. Early Failure Detection and Management
Effective early failure detection and management are crucial for enhancing Mean Time Between Failures (MTBF) by addressing issues before system failures. Incorporating advanced monitoring technologies like Edge Delta plays a vital role in this proactive approach.
Moreover, deploying IoT sensors provides real-time monitoring of critical parameters such as temperature and vibration. Complementing these sensors, machine learning algorithms analyze the collected data to predict potential failures, adding a layer of predictive maintenance.
Establishing an automated alert system is also essential to ensure timely responses to failure predictions. Configure these systems to trigger notifications when they detect abnormalities, enabling immediate maintenance actions.
Tips and recommendations:
- Implement IoT sensors: Continuously monitor key parameters like temperature and vibration, allowing for early anomaly detection.
- Employ predictive analytics: Use machine learning to analyze sensor data and predict potential issues.
- Automate alerts: Set up an automated system to immediately notify maintenance teams of detected abnormalities.
- Maintain sensor accuracy: Regularly calibrate and maintain sensors to ensure data reliability, which is crucial for effective monitoring.
- Integrate and visualize data: Centralize data from various sources for better analysis and employ visualization tools to identify and address issues quickly.
- Train staff regularly: Keep staff updated with the latest technologies and response strategies.
- Run simulations: Regularly simulate potential failure scenarios to test system responsiveness and refine emergency procedures.
Conclusion
MTBF is a crucial metric for determining the reliability of systems and component reliability. A higher MTBF keeps your systems running and your customers satisfied with your services. It enables engineers and decision-makers to identify issues, plan maintenance schedules, and enhance system design.
Understanding and calculating MTBF is critical for any organization that values reliability and productivity. By implementing strategies and following best practices for a good MTBF, an organization can reduce downtime, increase productivity, and, ultimately, reduce operational costs.
FAQs on How To Reduce MTBF
How to reduce MTTR and increase MTBF?
To reduce MTTR, you can control your expenses, minimize the impact on production, optimize resource usage, and improve operational efficiency. Regular inspections and condition monitoring increase MTBF and reduce repair time.
How to improve MTBF of machine?
To improve the MTBF of a machine, regularly maintain it using high-quality parts. Additionally, ensure correct installation and operation, employ predictive maintenance techniques, and train staff effectively to recognize and handle potential issues early.
How do you solve MTBF?
The MTBF is calculated by dividing the total time a piece of equipment is running by the number of breakdowns. The most commonly used unit of measurement for MTBF is hours.
What are the factors affecting MTBF?
Significant factors affecting MTBF include operational conditions, environmental factors, maintenance, and design. These factors can have significant impacts on the reliability and longevity of products.
Sources